What is Reverse Logistics?
Reverse logistics involves the process of returning products to the manufacturer after they have reached the market, either for refurbishment or salvaging parts. This process can be complex and costly for businesses that must set up dedicated teams and departments to handle returns efficiently. At RiverSide Integrated Solutions, we understand the challenges our customers face, which is why they turn to us for expert reverse logistics management.
To reap the benefits of reverse logistics, resources are needed for warranty tracking, returns management, and procuring additional parts when refurbished ones aren't available. Furthermore, the repair and rework aspects of reverse logistics demand highly skilled technical staff with troubleshooting expertise, knowledge of diagnostic equipment and a deep understanding of various engineering domains.
RiverSide Integrated Solutions offers small and mid-sized OEMs a solution to efficiently recapture product value. By outsourcing their reverse logistics to us, they gain access to top-notch technical and logistical expertise, allowing them to redirect their focus toward product improvements, customer service and new product launches. With us, they find peace of mind, knowing their reverse logistics are in capable hands.
The Benefits of Reverse Logistics
Customer Satisfaction and Loyalty
Save Time and Money
Better Sustainability
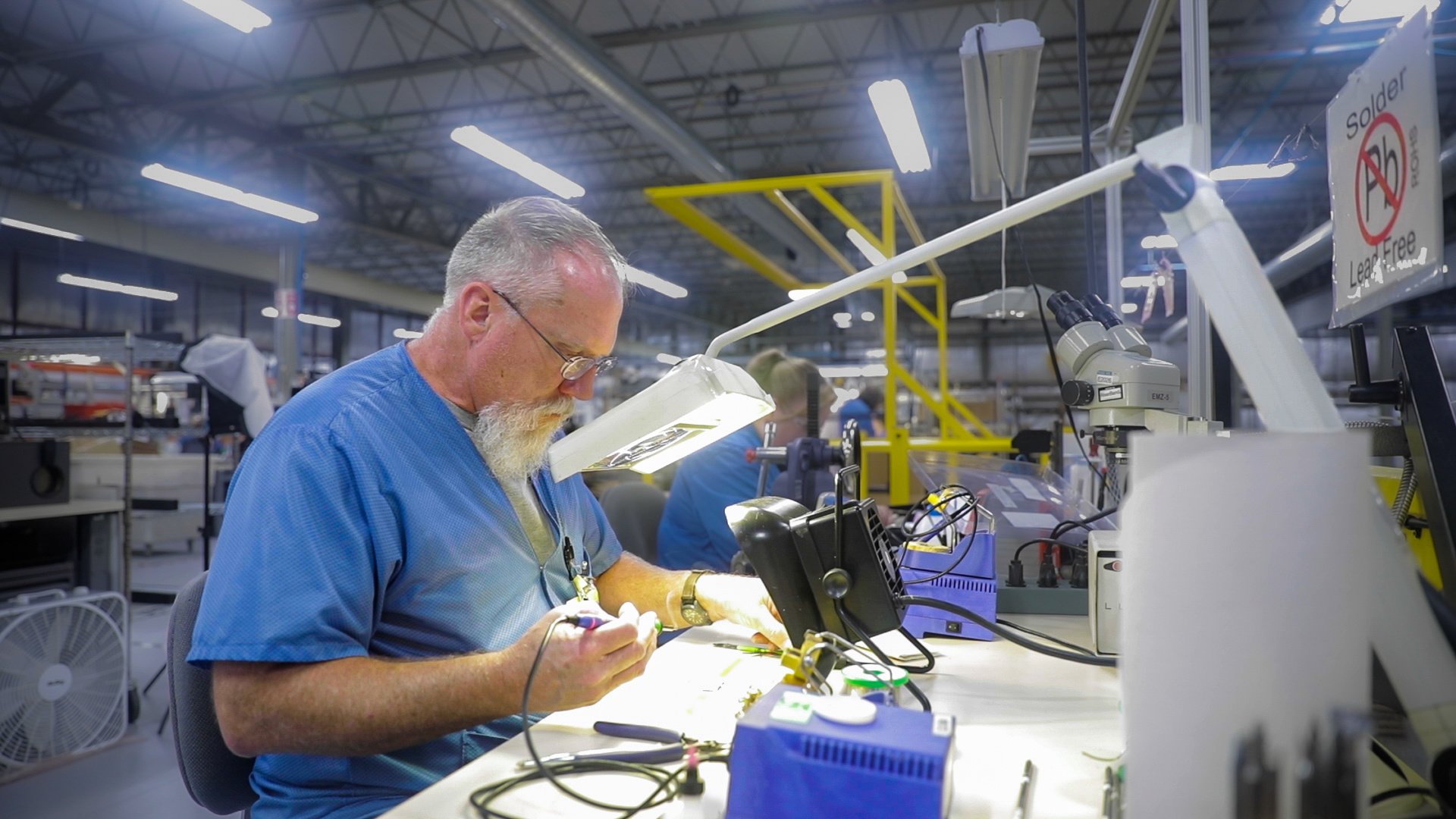
Refurbishment Solutions
- Diagnostic testing
- Circuit board component troubleshooting and replacement
- OEM replacement parts procurement
- Warranty claims management
Our Specialties
- Mechanical Assemblies
- Electromechanical Assemblies
- Electronic Assemblies
- Hydroelectric Assemblies
- Box Builds
- Systems Integration