In today’s modern world, we rely on electronics for most of our daily lives. Electronics find a place in almost every moment of our day, from cell phones to laptops to cars. Because of their comprehensive prevalence, electronics must meet a broad range of forms and functions.
However, electrical systems and devices are vulnerable to damage from many sources, both natural and artificial. Because of this, putting as much thought into constructing electronic protection as the electronics themselves is necessary. Natural particulates, moisture and temperatures can quickly compromise electronics utilized in outdoor environments. This is where electronic ruggedization adds value.
Ruggedized manufacturing is critical for various industries. They can be found anywhere circuit boards, electronics and electromechanical parts must operate in harsh, long-term environments. Ruggedization allows complex electronics to work reliably, even in challenging environments.
Situations with foreign elements like electromagnetic fields, vibrations or manufacturing particulates can cause degradation and poor function from exposure.
At RiverSide Integrated Solutions (RIS), we have the experience and equipment to protect electronics used in high-stress situations. Your assemblies can withstand the harshest conditions with our expertise and extensive ruggedized electronics capabilities. We can help you find the method that best applies to the operating environment of your device.
Watch this short video to learn more about our PCB potting and conformal coating techniques.
What Are Ruggedized Devices?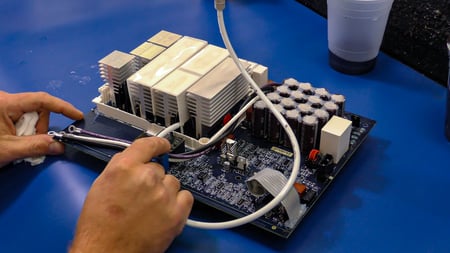
What Environments Require Ruggedized Devices?
Ruggedized electronics’ designers typically make them to withstand one or more of these harsh conditions. It is important to note that the list of extreme operating conditions is extensive. In most cases, devices can only withstand some of these factors.
A lot goes into the design of electronics that must withstand severe conditions. Thus, you’ll need to consider specific environmental factors when designing a given ruggedized device. You’ll want to create the most compact and cost-effective electronic for your application.
Design considerations for ruggedization are much more thorough than just the outer covering for the device. It often includes the enclosure, board mounting style, components and protective coatings.
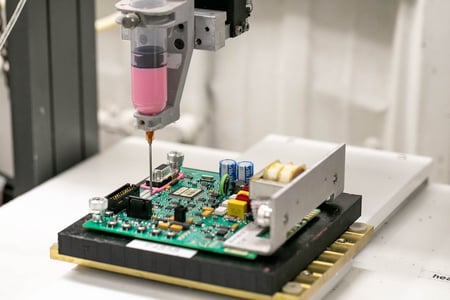
RIS Ruggedized Solutions to Protect Your Electronics
When you partner with RIS for your ruggedized electronics, you can protect your assemblies through the following ruggedization services.
CONFORMAL COATING AND POTTING
The material works to fit the contours of a board, protecting the components from external elements. We can fill complete electronic assemblies with epoxy, urethane and silicone compounds. This protects from shock, vibration, moisture and corrosion.
Low-Pressure Molding
This technology utilizes high-performance adhesives and can be an effective alternative to epoxy potting. Our low-pressure molding technology (MoldMan at 30 to 300 PSI) uses high-performance adhesives to encapsulate and protect components. Some of the materials used for this include polyolefin and polyimide.
They protect from particulates, moisture and vibrations.
CIRCUIT BOARD ENCLOSURE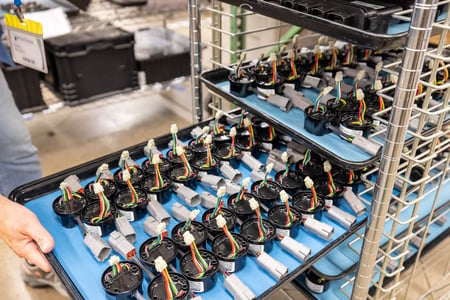
These specialty vaults shield assemblies against electromagnetic damage by blocking EMI activity with barriers of conductive and magnetic materials.
By isolating electrical devices with EMI shield enclosures, assemblies can operate in the long term. This includes industrial settings with high electromagnetic frequencies.
RIS is an advanced contract manufacturer providing robust solutions in circuit board assembly and product assembly. We employ more than 350 people and provide services to OEMs worldwide. We operate two state-of-the-art manufacturing facilities within the US.
With all of the choices in contract manufacturers out there, we know it can be challenging to find someone who understands your business model and has your best intentions in mind. RIS has always proven to be a win-win-focused relationship.
As your one-stop shop, we have the capabilities, capacity, quality assurance standards and resources to support all of your manufacturing needs. We understand that supply chain management is complex and very time-consuming, so we urge our customers to utilize us in the fullest capacity.
Our total-package solutions include:
- Dedicated Program Team
- Extensive supply-chain network for efficient parts procurement and kitting
- Subassembly and full box-build
- Warehousing and drop-shipping capabilities
- Reverse logistics
- Flexible order fulfillment
- Scalability to meet your needs
Contact us today at (507) 523-3220 to see how we can help with your manufacturing project, or click contact us for a quote.