Many original equipment manufacturers (OEMs) have adopted lean manufacturing as a keystone for success in today’s market. A lean manufacturing approach offers companies an array of benefits.
When lean principles are applied, sources of waste are reduced or even eliminated. This improves operations efficiency and product quality – adding significant value for customers. With shorter production times, manufacturers are more nimble and able to respond to customer needs and market conditions.
Additionally, lean strategies can be applied to supply chain and product development processes. This leads to quicker speed to market and a significant competitive advantage.
Whether OEMs perform production in-house or outsource to a contract manufacturer, they need to understand lean principles.
At RiverSide Integrated Solutions (RIS), we utilize lean principles to our teams a competitive edge.
The 5 Key Principles of Lean Manufacturing
Lean principles focus on streamlining production to improve value and productivity while minimizing waste. From a lean perspective, waste is anything that does not add value.
Below are the five fundamental principles of lean manufacturing. Lean manufacturing can significantly enhance efficiencies and productivity gains that lower production costs. That’s why it’s so important that contract manufacturers effectively implement these concepts. Lean provides the advantage companies seek.
Manufacturers from every sector have successfully applied these principles.
1. DEFINE VALUE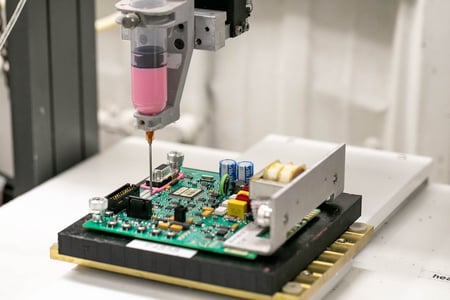
This lean manufacturing principle takes as its base the way customers define “value.” The value points for lean need to be clearly defined and communicated. It’s nearly impossible for contract manufacturers to streamline the manufacturing process if they aren’t.
Value requires designing and manufacturing products that meet customers’ needs and remove unnecessary features or “extras”.
Design for manufacturability (DFM) is a process often used to identify and eliminate waste in design and production. DFM is designing a product for easy manufacturing and creating a better, more cost-effective product.
It is a vital product-development step that simplifies and optimizes the design. This ensures high quality and efficiency during production and integrity once in the field.
DFM aims to reduce manufacturing costs and avoid costly disruptions without sacrificing quality or performance.
Visit our website for additional tips on incorporating DFM into lean manufacturing.
2. VALUE STREAM
This step involves mapping out the processes contributing to the value stream from beginning to end. It often starts with raw material acquisition and ends when the customer receives the final product.
Once you’ve mapped your value stream, it is easier to identify and address steps that do not add value. This is a critical aspect of lean manufacturing. The purpose is to identify potential waste areas and work to reduce or eliminate the waste.
Identification and elimination of waste are crucial to the success of lean manufacturing. Contract manufacturers often identify several types of waste when they apply a lean approach.
Below are some of the most common approaches.
WAITING
This applies to personnel or machinery. When workers spend time waiting for machines to be available or materials to arrive, there is room for improvement.
UNOPTIMIZED INVENTORY
Too much or too little inventory leads to inefficiencies and waste.
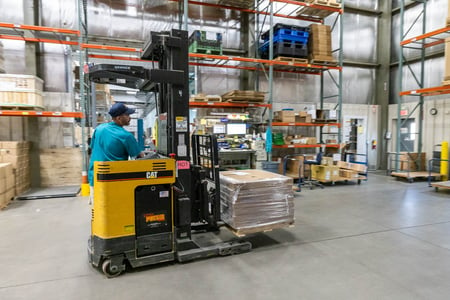
INEFFICIENT LOGISTICS
Logistics includes the workflow of the product on the manufacturing floor. Still, it extends beyond the facility to acquire raw materials and transport the final product to the customer.
OVER-PROCESSING OR OVER-ENGINEERING
The objective of manufacturing is to meet specifications per the agreed-upon design. There is often a significant amount of wasted time, equipment and resources spent on over-engineering and over-processing a product.
UNNECESSARY MOTION
This can be wasted motion of personnel or equipment. Reducing unnecessary movement is key to improving the entire manufacturing supply chain. Facilities that are organized and laid out well excel in this area.
DEFECTS OR OTHER QUALITY ISSUES
Quality teams need to spend time building their quality control processes into production properly. If they don’t, scrapping and reworking off-spec products can be a massive area of waste.
3. CREATE FLOW
Once teams have streamlined processes to remove waste, operations should run more smoothly and efficiently. This improves product flow. Efficient product flow requires items to move with minimal delays or interruptions. It looks at all the steps of the manufacturing process. This includes procurement to production to secondary operations to packaging to customer delivery with minimal delays or interruptions.
Contract manufacturers that apply lean manufacturing principles should follow raw materials throughout the manufacturing process. This will help them better understand areas for improvement. It will also help them optimize the facility layout, materials handling and personnel touch points for success.
A well-organized manufacturing facility achieves efficient product flow, reducing production times and inventory requirements.
4. ESTABLISH PULL
With the process running more smoothly, contract manufacturers can use a pull-based production system – another principle of lean manufacturing.
Products can be manufactured and delivered “just in time,” reducing inventory requirements and costs. This also results in a shorter time to market, further driving competitiveness.
The key to pulling systems is to have the right materials in the right quantity at the right time. This is very similar to Just-in-Time (JIT) manufacturing. In short, it’s about producing only the required volume at the right time.
With JIT, order placement triggers the manufacturing process for products. This type of manufacturer keeps raw material and final product levels low. This reduces waste on surplus inventory and avoids overproduction.
Comparatively, with traditional push manufacturing systems, a supply purchase triggers the process. This then pushes material through the process even when an order may not exist.
These push systems are easier to create. However, they often result in more extensive inventories and other waste.
5. SEEK PERFECTION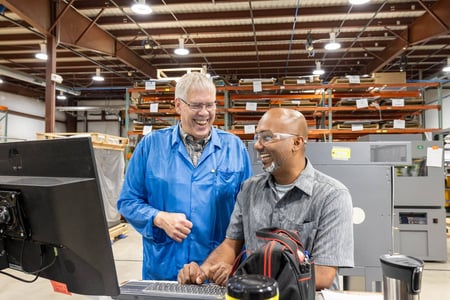
The final principle is to seek perfection. This concept is about continuous improvement. Lean manufacturing is an ongoing assessment to avoid waste and inefficiencies from creeping back into the process.
This principle often seems easy but is very difficult to implement. It requires contract manufacturers to be diligent continuously – not just for a fixed period.
One way to seek perfection is with the company culture. Companies with a lean culture ensure that all personnel are empowered to participate in continuous improvement efforts. All levels of the organization must participate in the lean culture, from management to the production floor.
At RIS, a key focus of our lean manufacturing approach is maximizing customer value while minimizing waste. We empower every employee to make a difference by coming forward with suggested improvements.
About RiverSide Integrated Solutions:
RIS is an advanced contract manufacturer providing robust solutions in circuit board assembly and product assembly. We employ more than 350 people and provide services to OEMs worldwide. We operate two state-of-the-art manufacturing facilities within the US.
With all of the choices in contract manufacturers out there, we know it can be challenging to find someone who understands your business model and has your best intentions in mind. RIS has always proven to be a win-win-focused relationship.
As your one-stop shop, we have the capabilities, capacity, quality assurance standards and resources to support all of your manufacturing needs. We understand that supply chain management is complex and very time-consuming, so we urge our customers to utilize us in the fullest capacity.
Our total-package solutions include:
- Dedicated Program Team
- Extensive supply-chain network for efficient parts procurement and kitting
- Subassembly and full box-build
- Warehousing and drop-shipping capabilities
- Reverse logistics
- Flexible order fulfillment
- Scalability to meet your needs
Contact us today at (507) 523-3220 to see how we can help with your manufacturing project, or click contact us for a quote.