Nothing is 100% perfect 100% of the time. Because of this, the best manufacturers design their systems to examine the failure modes thoroughly when they happen. This allows them to trace them back to a root cause and eliminate those failures. When we talk about printed circuit board (PCB) failures, there are two distinct types to consider. There are failures during the design-build-test cycle and failures during service. Of course, the customer is only concerned about failures in service.
However, to minimize these, we often need to create failures during the design-build-test cycle. This will identify weaknesses and shore them up before the product design is ready for production.
RiverSide Integrated Solutions (RIS) provides full-circuit board and electromechanical assembly with testing capabilities. We can develop and test circuit board inspection and testing schemes to ensure the product performs well.
We can perform PCB assembly (PCBA) testing, system-level integration testing and thermal/mechanical stress testing. Whatever your requirements, we can ensure it works properly. All of this adds up to a robust manufacturing process and high reliability in service.
ELECTRICAL ISSUES
If we look at the manufacturing process first, there are a couple of things that can show up.
ALIGNMENT AND VIAS
If your application requires a multi-layer board, the alignment from layer to layer is critical. There are often vias (small conductive channels that act as conductors) between layers. It’s easy to imagine how a misalignment between layers can lead to a short or open circuit.
COMPONENT PLACEMENT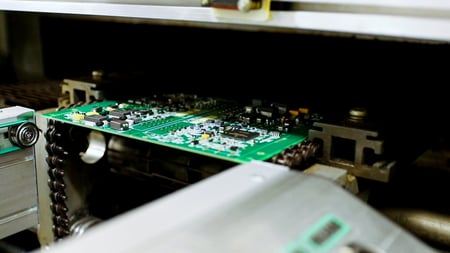
Misalignment is also a critical process for the placement of components. They can be as small as a fraction of a millimeter in size. Suppose you add in the small area available for solder placement. In that case, solder bridges (shorts) or open circuit conditions can occur.
Fortunately, at RIS we use an automated handling system for PCBAs with a fully Automated Optical Inspection (AOI) system. This system rapidly takes snapshots at various stages of assembly. It compares critical real-time parameters such as solder coverage and component placement before moving the board to the next level.
As a result, we eliminate manufacturing errors before the board goes to the next step. That means they seldom appear in the finished board assembly.
We can offer a functional, custom, end-of-line tester in certain instances. These testers would power up the board, inject appropriate signals into the circuitry and measure the response. This would constitute a final or acceptance test before packaging and shipping.
MECHANICAL ISSUES
Although PCBAs are considered strictly electrical in function, they must also handle some surprisingly tough mechanical issues.
THERMAL STRESSES
One of the simplest to understand is the complications of mixing different materials. PCBAs have various materials in their makeup: copper, epoxy, solder, ceramics and plated metals. Each component expands when heated and shrinks as it cools.
Everything on the board undergoes tens of thousands of cold-hot cycles during their lifetime, so everything must be tested. This includes all of the solder joints, attachment points, the laminations of the board and connectors.
If the board is used outdoors, these temperature swings could easily be 100 ˚C for several days. Over time, these temperature-related stresses can lead to cracking and loss of proper electrical function.
A common way to guard against this failure mechanism is by burning-in boards. This test subjects a PCBA to a temperature regime that allows all components to “adjust” to temperature-related stresses.
There are a couple of ways to do this, depending on the experience of the board designer. A high-temperate soak, often for 24 hours, performs an annealing process. This makes the PCBA much more immune to cracking later.
Another approach is to have the boards cycle through temperatures from the lowest to the highest operating temperatures. This test gives the PCBA time to soak at both the cycle’s hot and cold ends. This is a more stressful thermal test and can weed out product at the very end of the bell curve. RIS can accommodate either type of thermal conditioning, depending on your needs.
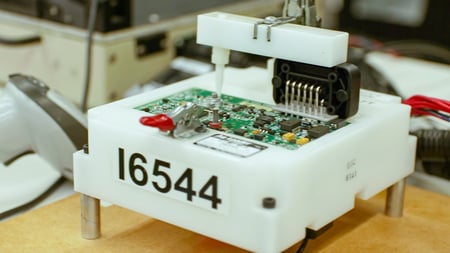
SHOCK AND VIBRATION
The other mechanical issue that a PCBA may have to endure is a high shock and vibration. This usually requires stiffening up the board through mechanical supports. Alternatively, the board can be mounted on shock absorbers to isolate it from the outside forces.
Usually, either of these approaches is used with added epoxy around the heavier components to prevent them from loosening. The design can be validated against this vibration environment using standard “shock and vibe” test equipment and fixtures.
FIELD FAILURES
As you can imagine, after such a thorough manufacturing process, most PCBAs are ready for a long service life. And you would be right – electrical assemblies are considered a highly reliable part of any system.
At the same time, some products fail in service. Usually, when this happens, it is within the first few weeks, especially if the part is a replacement. There are many explanations for this, but we can illustrate with a simple example.
REPLACEMENT PROCEDURE
For a correct replacement procedure, technicians must wholly replace old parts. The technician will begin by disconnecting old parts. They will then clean and inspect the board for cracking or wear and tear. Finally they will check electrical connections for continuity.
If they don’t properly follow these steps, later service calls often find intermittent electrical connection issue or voltage drops. In retrofit situations, sometimes the power connector has been replaced. Here, it often becomes necessary to modify the replacement part to match the existing installation.
Unfortunately, the power line often gets miswired, and the unit dies in a puff of smoke. These are usually honest mistakes. Well-meaning people try to solve a problem quickly and overlook a critical defect.
Usually, a phone call to the technical support line before doing the replacement will weed these out. This saves everybody time in the long run.
There are, of course, legitimate premature field failures that need to be treated seriously. Where RIS has the service contract, give us a call. We perform reverse logistics services for all of our customer’s needs.
RIS PCBA EXPERTISE
At RIS, PCB assembly is one of our core competencies. We provide reliable, seamlessly-assembled printed circuit board systems built with extreme precision.
Our skilled engineers, technicians and assemblers work to expertly put together a complete PCBA. When you choose RIS, you can expect the hands-on customer care of a small operation with the capabilities characteristic of a larger company. We provide our complete electronics manufacturing services for OEMs in any industry.
Our electronics assembly expertise includes:
- Surface Mount Technology (Fine-pitch, BGA (1 mm), µBGA (.4 mm), 01005, X-Ray, automated rework, and automated optical inspection (AOI)
- Magazine to Magazine handling
- Smart Shelving floor stock inventory control
- X-ray reel counting
- Lead-through auto-insertion (Axial, Radial, DIP, and Zierick Terminals)
- Wave Solder and Selective Solder Machines (No-clean & aqueous flux processes) RoHS and Tin/Lead capabilities
- Special Application Equipment (Cobot dispensing systems)
- Conformal coating (Silicone, Urethane)
- Potting (Epoxy, Urethane, and Silicone)
- Low-pressure molding technology
- Comprehensive product testing
- 3D Printing
About RiverSide Integrated Solutions:
RIS is an advanced contract manufacturer providing robust solutions in circuit board assembly and product assembly. We employ more than 350 people and provide services to OEMs worldwide. We operate two state-of-the-art manufacturing facilities within the US.
With all of the choices in contract manufacturers out there, we know it can be challenging to find someone who understands your business model and has your best intentions in mind. RIS has always proven to be a win-win-focused relationship.
As your one-stop shop, we have the capabilities, capacity, quality assurance standards and resources to support all of your manufacturing needs. We understand that supply chain management is complex and very time-consuming, so we urge our customers to utilize us in the fullest capacity.
Our total-package solutions include:
- Dedicated Program Team
- Extensive supply-chain network for efficient parts procurement and kitting
- Subassembly and full box-build
- Warehousing and drop-shipping capabilities
- Reverse logistics
- Flexible order fulfillment
- Scalability to meet your needs
Contact us today at (507) 523-3220 to see how we can help with your manufacturing project, or click contact us for a quote.