Printed circuit boards (PCBs) continue to grow in complexity. Because of that, PCB assembly has become an even more critical to electronics manufacturing. Even the slightest assembly error could lead to poor performance or failure. That’s why surface mount technology (SMT) has become a cornerstone of modern electronics manufacturing.
Because it’s highly automated and precise, SMT enables more reliable assemblies at a reduced weight, volume and cost. This makes it an excellent choice for most electronics assembly, especially high-volume production. It is a great option for electronics needing a high density of components or requiring a smaller, lighter board.
Given the criticality of this step, many original equipment manufacturers (OEMs) look to outsource. It is imperative that they partner with a knowledgeable contract manufacturer like RiverSide Integrated Solutions (RIS). At RIS, we have the requisite experience and proven processes to guide OEMs through the PCBA process. We can help you select the right assembly technologies to ensure success in the field.
Before diving deeper into SMT, it will be helpful to better understand where it fits in the PCBA process.
Main Steps in the PCBA Process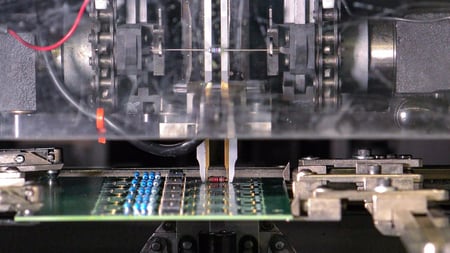
Below are the primary steps in the PCB assembly process. The steps and sequencing may vary slightly depending on whether SMT or through-hole technology (THT) are employed. Some may even employ both! However, the following describes the key elements of any PCBA process.
1. APPLY SOLDER PASTE
The first step in PCBA is to apply the solder paste. It is applied to the sections of the PCB where components will be mounted. The paste is a mixture of solder and flux used to join the parts to the board permanently.
2. PLACE THE COMPONENTS
The next phase is to place the necessary components on top of the solder paste. This step is often called “pick and place.”
There are many different types of components for PCB, depending on functionality. Some of the most common are resistors, capacitors, inductors or sensors.
3. SOLDERING
This step’s purpose is to bond the components to the PCB permanently.
SMT typically utilizes a reflow oven and conveyor system to melt the existing solder paste. Selective soldering machines are also becoming more popular. They are capable of precisely soldering boards with smaller and more complex layouts.
With THT, the components have leads that go through existing holes on the board. A wave soldering method is the most common way to solder these boards. A wave solder machine uses a wave of molten solder that flows across the bottom of the board.
In both cases, the molten solder joins the components and leads to the board. The assembly is then cooled to solidify the solder again and fix the parts.
4. INSPECT THE ASSEMBLY
This phase of the PCBA process is crucial. Proper inspection is necessary to ensure production staff and machines performed prior steps effectively. This step may entail both manual and automatic inspections.
5. TESTING
The final step in the PCBA process is testing to ensure the PCB functions as designed. There are various test methods, such as flying probes, in-circuit testing, and others. The PCBA process is complete once testing is done.
What Exactly is Surface Mount Technology?
As noted, SMT is a widely utilized soldering method for PCBA. As the name implies, SMT attaches components directly to the surface of the PCB. It does so using tiny amounts of solder paste and does not require any holes in the board.
In an SMT PCBA, the solder joint forms the physical and mechanical connections. Electronics made via SMT are called surface mount devices. SMT allows components to be mounted to both sides of the board. This allows for more components on a given board and smaller PCBs compared to one using THT.
SMT often involves automated equipment that position and mount the components on the board.
For more details about SMT at RIS, watch our short video.
Advantages of SMT
There are many advantages to using SMT during PCB assembly. Below are some of the key benefits.
INCREASED COMPONENT DENSITY
SMT components’ geometric size and volume are typically less than THT components. For this reason, SMT can fit a larger number of components on a PCB surface. This enables designers to create boards with high component density.
Electronics continue to shrink in size, while the demand for more functionality increases. This means that SMT capabilities are only becoming an even larger advantage. With SMT, manufacturers can create higher-density PCBs.
INCREASED EFFICIENCY AND THROUGHPUT
Elements of SMT are often automated, which enables rapid and precise mounting of the components on the board. This leads to efficiency gains that allow for higher production volumes while maintaining excellent reliability.
Higher throughput of PCBs also results in lower board costs – another big advantage of SMT.
SMALLER, LIGHTER WEIGHT PCBS
SMT can utilize smaller and lighter components compared to THT. This enables SMT to create compact PCBs that maximize the space on the board without sacrificing functionality and performance.
Lighter-weight PCBs are an important advantage of SMT for industries where weight is critical, such as aviation.
SIMPLER PCBA
THT assembly method requires component leads be bent into shape and inserted into holes drilled in the PCB solder joints. Conversely, SMT mounts components to the board without much drilling. This leads to a much simpler and faster PCB assembly process.
Additionally, SMT does not require lead forming since leads are surface mounted to the pads. For these reasons, SMT makes PCBA much faster and less prone to error than THT.
SUPERB RELIABILITY
Surface-mounted components are often more reliable than through-hole components. In particular, SMT components are less prone to failure due to vibration, shaking and shock.
MIXED TECHNOLOGY BOARDS
SMT and THT components can co-exist on a single board. This enables designers to create electronics that employ both methods during PCB assembly. This may be necessary for designs where space constraints require using both connectors.
RIS PCBA EXPERTISE
At RIS, PCB assembly is one of our core competencies. We provide reliable, seamlessly-assembled printed circuit board systems built with extreme precision.
Our skilled engineers, technicians and assemblers work to expertly put together a complete PCBA. When you choose RIS, you can expect the hands-on customer care of a small operation with the capabilities characteristic of a larger company. We provide our complete electronics manufacturing services for OEMs in any industry.
Our electronics assembly expertise includes:
- Surface Mount Technology (Fine-pitch, BGA (1 mm), µBGA (.4 mm), 01005, X-Ray, automated rework, and automated optical inspection (AOI)
- Magazine to Magazine handling
- Smart Shelving floor stock inventory control
- X-ray reel counting
- Lead-through auto-insertion (Axial, Radial, DIP, and Zierick Terminals)
- Wave Solder and Selective Solder Machines (No-clean & aqueous flux processes) RoHS and Tin/Lead capabilities
- Special Application Equipment (Cobot dispensing systems)
- Conformal coating (Silicone, Urethane)
- Potting (Epoxy, Urethane, and Silicone)
- Low-pressure molding technology
- Comprehensive product testing
- 3D Printing
About RiverSide Integrated Solutions:
RIS is an advanced contract manufacturer providing robust solutions in circuit board assembly and product assembly. We employ more than 350 people and provide services to OEMs worldwide. We operate two state-of-the-art manufacturing facilities within the US.
With all of the choices in contract manufacturers out there, we know it can be challenging to find someone who understands your business model and has your best intentions in mind. RIS has always proven to be a win-win-focused relationship.
As your one-stop shop, we have the capabilities, capacity, quality assurance standards and resources to support all of your manufacturing needs. We understand that supply chain management is complex and very time-consuming, so we urge our customers to utilize us in the fullest capacity.
Our total-package solutions include:
- Dedicated Program Team
- Extensive supply-chain network for efficient parts procurement and kitting
- Subassembly and full box-build
- Warehousing and drop-shipping capabilities
- Reverse logistics
- Flexible order fulfillment
- Scalability to meet your needs
Contact us today at (507) 523-3220 to see how we can help with your manufacturing project, or click contact us for a quote.