In our world. technological progress is often measured in leaps and bounds. To this end, the electronics manufacturing industry stands as a testament to relentless innovation and adaptation. Over the past four decades, this industry has undergone remarkable transformations. Most of these transformations have been driven by advancements in technology. They’ve also been affected by changing market dynamics and evolving consumer demands.
For the past 40 years, RiverSide Integrated Solutions (RIS) has been at the forefront of the electronics manufacturing industry. In honor of the company’s anniversary, Steve Craney, founding member and owner of RIS, delved into how things have changed.
FROM SWAGED LEADS TO SURFACE MOUNT TECHNOLOGY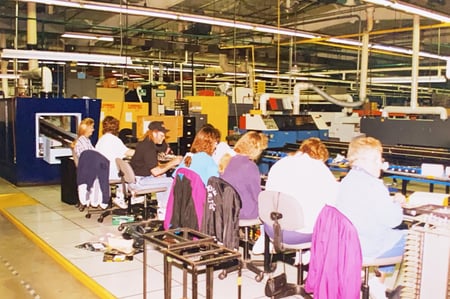
The journey begins in the early 1980s, where electronics manufacturing was characterized by the use of through-hole (TH) technology. Devices were constructed by placing components on the board with leads that passed through the circuit board. Original equipment manufacturers (OEMs) often still required swaged ends for stability, despite emerging evidence that soldering alone was reliable.
Swaging is a process involved in TH printed circuit board assembly (PCBA). In this process, component leads are either cut with a flat end or bent over and cut before soldering. The swaged end keeps the component from going back through the hole even if the solder fails. Because of the complexity of this process, skilled technicians were required to meticulously cut and solder components into place.
Steve Craney recalls transitioning from TH boards to surface mount technology (SMT) as a pivotal moment. “They were just getting away from [swaged leads] when we started this business. Some people wanted swaged leads; some people didn’t care, as long as they were soldered.”
SMT revolutionized the manufacturing process by allowing components to be mounted directly onto the surface of the circuit board. This eliminated the need for leads to pass through the board. This shift improved assembly efficiency and enabled the production of smaller and more compact electronic devices.
QUALITY CONTROL AND TESTING
Another significant change observed in electronics manufacturing was the evolution of quality control and testing methodologies. In the early days,
burn-in processes were commonplace. In this practice, newly manufactured devices were subjected to extended periods of operation to identify potential failures. However, advancements in testing equipment and techniques led to the adoption of more efficient testing protocols. Steve Craney remarked, “A good functional test, or a good test where you have power on it for 5 to 10 minutes, is just as good.”
Industry leaders implemented functional testing as an alternative to burn-in procedures, marking a paradigm shift in the industry. Functional testing focuses on assessing device performance under real-world conditions within shorter timeframes. This streamlines the manufacturing process and reduces costs associated with prolonged testing periods.
AUTOMATION AND ROBOTICS
The integration of automation and robotics played a crucial role in enhancing manufacturing efficiency and precision. In the mid-1990s, the introduction of advanced assembly machines revolutionized production lines with their robust construction and high-speed capabilities. These machines, characterized by their solid steel frames and precise movement mechanisms, set new standards for reliability and productivity in electronics manufacturing.
Furthermore, the innovations of companies like United Shoe and Universal, who created breakthrough technology for auto-insertion, further propelled the automation trend. These advancements not only accelerated production rates but also ensured consistent quality across manufacturing processes.
CHALLENGES AND OPPORTUNITIES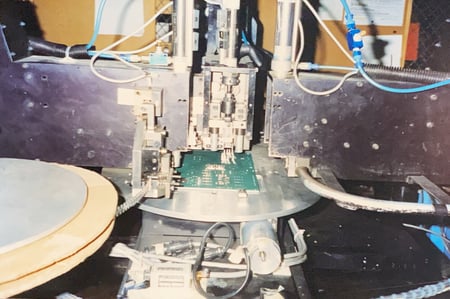
While technological advancements have propelled the electronics manufacturing industry forward, they have also presented unique challenges and opportunities. The rise of offshore manufacturing and intense global competition has exerted pressure on margins. This has driven the need for greater operational efficiency and cost-effectiveness.
However, amidst these challenges, opportunities abound for companies that embrace innovation and adaptability. Steve Craney emphasizes that importance of staying ahead of technological breakthroughs, particularly in the era of artificial intelligence (AI). He states that, “The company that can stay very innovative will win in this battle . . . that’s the weakness of AI.”
AI holds the potential to revolutionize various aspects of manufacturing. These include process optimization and predictive maintenance. However, its implementation requires a strategic approach that balances the strengths of AI with the innovative capabilities of humans.
LOOKING TOWARDS THE FUTURE
As the industry continues to evolve, the key to sustained success lies in fostering a culture of innovation and collaboration. With a dedicated team of professionals committed to staying abreast of emerging technologies, RIS is poised to navigate the ever-changing landscape of electronics manufacturing.
The past four decades have witnessed remarkable transformations in the electronics manufacturing industry. As we look towards the future, the journey of electronics manufacturing promises innovation, adaptation and endless possibilities.
About RiverSide Integrated Solutions:
RIS is an advanced contract manufacturer providing robust solutions in circuit board assembly and product assembly. We employ more than 350 people and provide services to OEMs worldwide. We operate two state-of-the-art manufacturing facilities within the US.
With all of the choices in contract manufacturers out there, we know it can be challenging to find someone who understands your business model and has your best intentions in mind. RIS has always proven to be a win-win-focused relationship.
As your one-stop shop, we have the capabilities, capacity, quality assurance standards and resources to support all of your manufacturing needs. We understand that supply chain management is complex and very time-consuming, so we urge our customers to utilize us in the fullest capacity.
Our total-package solutions include:
- Dedicated Program Team
- Extensive supply-chain network for efficient parts procurement and kitting
- Subassembly and full box-build
- Warehousing and drop-shipping capabilities
- Reverse logistics
- Flexible order fulfillment
- Scalability to meet your needs
Contact us today at (507) 523-3220 to see how we can help with your manufacturing project, or click contact us for a quote.