Electronic technologies continue to advance while the demand for more functionality increases. Similarly, designs for printed circuit boards (PCBs) and components keep getting smaller and more complex. Because of these changes, PCB assembly (PCBA) has become an even more crucial step in electronics manufacturing. Even a small assembly error could lead to poor performance or failure of an electronic device in the field. Original equipment manufacturers (OEMs) must work hard to ensure their assemblies are of the highest quality.
As the manufacturing of PCBs becomes more complex, more OEMs are turning to outsourcing their assembly needs. Given the criticality of PCBA, they must find a reliable contract manufacturer for these services.
RiverSide Integrated Solutions (RIS) is a knowledgeable contract manufacturer with years of experience specializing in PCBA. RIS has the requisite experience and proven know-how to guide OEMs through the PCBA process. We can select the right assembly technologies to ensure success in the field.
Below are some of our PCBA best practices to ensure your PCBA goes smoothly.
CLEAR COMMUNICATION UPFRONT
The best way to avoid PCBA issues is to collaborate with your partner upfront – before the detailed design begins. OEMs must communicate the functionality requirements and application of the PCB. Clear communication allows OEMs to tap into the experience and expertise of their partner. This often results in a better design, as well as a better production and assembly plan.
DESIGN FOR MANUFACTURABILITY AND ASSEMBLY
The easier to manufacture a product is, the more efficiently the manufacturing operations can run. Companies use design for manufacturability and assembly (DFMA) assessment to identify production and assembly issues early on. The result is more cost-effective production, better quality and quicker speed to market.
Click here for additional tips on implementing DFMA in your PCB designs. Designing PCBs with assembly in mind is crucial yet is often overlooked – leading to significant challenges.
Below are 3 broad concepts best applied during the DFMA process:
MINIMIZE COMPLEXITY
The team should evaluate each feature and functional requirement of the PCB for complexity. The goal is to minimize complexity without sacrificing requisite functionality.
STANDARDIZE
The PCB should be designed with common components and sizes compatible with standard assembly processes when possible. This simplifies the procurement of parts and PCB assembly, and saves OEMs time and money.
Additionally, specialized components often have longer lead times. Because of this, teams must ensure procurement of the desired parts without sacrificing the project schedule
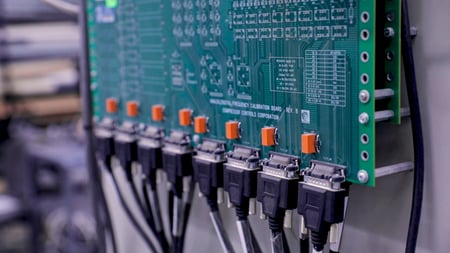
QUALITY
Finally, it’s important to remember that quality is not uniform across all PCB components and parts. Similarly, not all manufacturing partners assemble PCBs to the same degree of quality.
That’s why, it’s crucial to partner with a proven PCB assembler, like RIS. We have established quality control programs and a network of reliable suppliers. Let our years of hard work be your advantage!
RIS PCBA EXPERTISE
At RIS, PCB assembly is one of our core competencies. We provide reliable, seamlessly-assembled printed circuit board systems built with extreme precision.
Our skilled engineers, technicians and assemblers work to expertly put together a complete PCBA. When you choose RIS, you can expect the hands-on customer care of a small operation with the capabilities characteristic of a larger company. We provide our complete electronics manufacturing services for OEMs in any industry.
Our electronics assembly expertise includes:
- Surface Mount Technology (Fine-pitch, BGA (1 mm), µBGA (.4 mm), 01005, X-Ray, automated rework, and automated optical inspection (AOI)
- Magazine to Magazine handling
- Smart Shelving floor stock inventory control
- X-ray reel counting
- Lead-through auto-insertion (Axial, Radial, DIP, and Zierick Terminals)
- Wave Solder and Selective Solder Machines (No-clean & aqueous flux processes) RoHS and Tin/Lead capabilities
- Special Application Equipment (Cobot dispensing systems)
- Conformal coating (Silicone, Urethane)
- Potting (Epoxy, Urethane, and Silicone)
- Low-pressure molding technology
- Comprehensive product testing
- 3D Printing
About RiverSide Integrated Solutions:
RIS is an advanced contract manufacturer providing robust solutions in circuit board assembly and product assembly. We employ more than 350 people and provide services to OEMs worldwide. We operate two state-of-the-art manufacturing facilities within the US.
With all of the choices in contract manufacturers out there, we know it can be challenging to find someone who understands your business model and has your best intentions in mind. RIS has always proven to be a win-win-focused relationship.
As your one-stop shop, we have the capabilities, capacity, quality assurance standards and resources to support all of your manufacturing needs. We understand that supply chain management is complex and very time-consuming, so we urge our customers to utilize us in the fullest capacity.
Our total-package solutions include:
- Dedicated Program Team
- Extensive supply-chain network for efficient parts procurement and kitting
- Subassembly and full box-build
- Warehousing and drop-shipping capabilities
- Reverse logistics
- Flexible order fulfillment
- Scalability to meet your needs
Contact us today at (507) 523-3220 to see how we can help with your manufacturing project, or click contact us for a quote.